Metal forming: cold extrusion
Cold extrusion is a metal plastic forming process in which high pressure is applied to a metal blank through a die at room temperature or lower temperature to produce plastic deformation, thereby obtaining a part of the desired shape and size. Since no heating is required, cold extrusion has the advantages of high precision, high strength and high material utilization
Weforging has 5 sets of 35-800T cold extrusion equipment, which are mainly suitable for the manufacture of low carbon steel and aluminum alloy and precision parts such as barrel, gear, shaft and fasteners.

Add Your Heading Text Here
Advantages: High material utilization, excellent mechanical properties and environmental protection characteristics make it widely used in automotive, machinery, fasteners, electronics and other fields.
Application prospects: low precision gear and forging machining process products, gradually through cold extrusion to achieve, and then reduce the cost of production process, the future with the progress of mold technology and material science, cold extrusion will play a greater role in precision manufacturing.
▼Cold extrusion applications
Cold extrusion applications
Gear manufacturing: spur gear, spline shaft (such as small transmission gear).
Fasteners: bolts, nuts, rivets.
Auto parts: piston pin, universal joint, drive shaft.
Electronic appliances: connectors, heat sinks.
Cold extrusion is an efficient and high-precision metal forming process, which is especially suitable for mass production of ordinary precision gears, shafts, fasteners, tubes, etc.
Disadvantages of cold extrusion: the one-time investment cost of the mold is high, and there are certain requirements for batch;

▼Cold extrusion & hot forging
Cold extrusion & hot forging
✅ Cold extrusion advantage
High material utilization rate (up to more than 90%, much higher than cutting).
High strength: metal grain refinement, mechanical properties better than cast or machined parts.
High precision: dimensional tolerance up to IT8-IT9, surface roughness Ra 1.6-3.2μm.
High production efficiency: suitable for mass production of gear shaft, fastener, spline shaft.
❌ Disadvantages
High die cost: high strength die steel (such as SKD11, DC53), suitable for mass production.
High material requirements: high plastic materials (such as low carbon steel, aluminum alloy, copper alloy) are required.
Product part size

✅ Advantages of hot forging
Wide range of applicable materials: can forge high strength steel, alloy steel and other hard to deform metal.
Low deformation resistance: softened metal, temperature controllable.
Large workpieces can be manufactured: suitable for large forgings (such as flanges, connecting rods, gear rings).
Good microstructure uniformity: casting defects (porosity, shrinkage) can be eliminated at high temperatures.
❌ Limitations of hot forging
Low accuracy: tolerance IT12-IT14, require subsequent machining.
General appearance: oxide layer

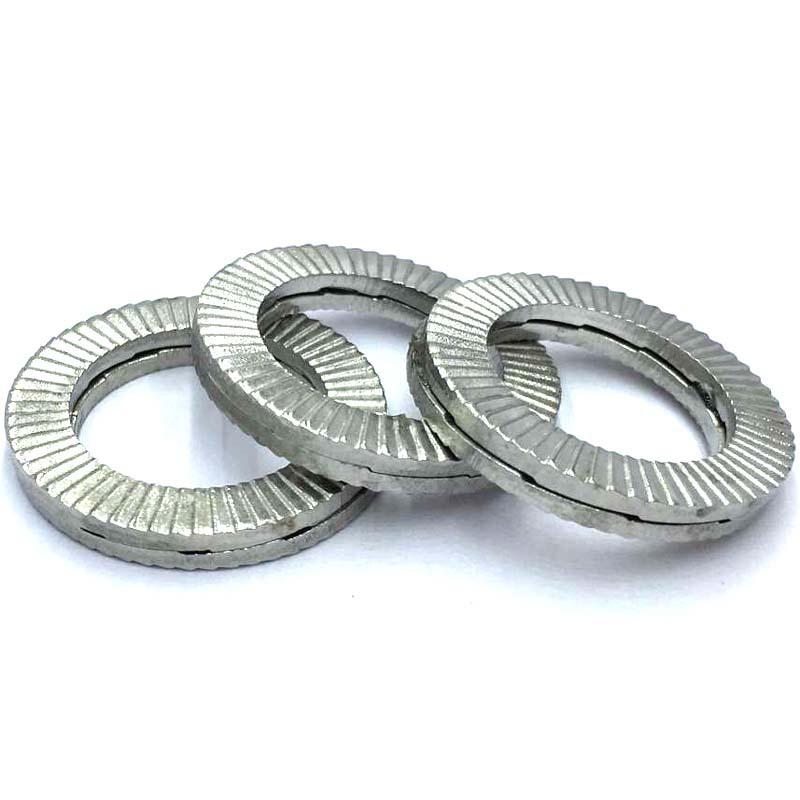
▼How to choose cold forging & hot forging?
In the metal forming process, Cold Extrusion and Hot Forging are both important metal forming processes, but their process characteristics, application scenarios and advantages and disadvantages are quite different:
Select the case of cold extrusion:
✔ Need high-precision, high-strength parts (such as precision gears, bolts, locknuts).
✔ Mass production (such as automotive fasteners), mold costs can be shared.
✔ The material is low carbon steel, aluminum alloy, copper alloy and other plastic metal.
Select the case of hot forging:
✔ Material for high-strength steel, alloy steel and other hard to deform metal.
✔ Large parts size (such as wind power gear blank, mining forgings, flange forgings, shaft gear forging blank).
✔ High requirements for internal structure density (such as transmission forgings that withstand high load impact).
We are a set of hot forging, cold forging, cold extrusion, gear forming processing, precision machining as one of the comprehensive process manufacturers, is your product process solutions to provide and manufacturers, this is why the international large manufacturing enterprises choose us, because we are professional, we will recommend manufacturing processes according to your products!